Expert Tips on Implementing Foam Control in Chemical Processing Environments
Expert Tips on Implementing Foam Control in Chemical Processing Environments
Blog Article
Understanding the Significance of Foam Control in Industrial Processes
In industrial processes, foam control is frequently a neglected yet crucial facet that directly affects functional effectiveness and item integrity. The existence of too much foam can result in significant obstacles, including disrupted blending and decreased reaction kinetics, which might eventually affect item high quality throughout various sectors such as pharmaceuticals and food manufacturing. Comprehending the nuances of foam administration, including reliable methods and prospective improvements, increases critical questions about ideal methods and future innovations. What are the implications for markets pursuing enhanced performance and conformity?

The Duty of Foam in Market
Foam plays a considerable role in numerous industrial processes, affecting both performance and item top quality. In markets such as food and drink, drugs, and petrochemicals, foam can offer both detrimental and beneficial purposes. In the food sector, foam stabilization is essential during processes like whipping cream or generating beer, where the top quality of foam straight impacts consumer perception and product features.
In chemical manufacturing, foam can function as a barrier, stopping the correct mixing of reagents, which can cause insufficient reactions and suboptimal yields. On the other hand, in procedures like flotation in mineral processing, foam is used to separate valuable minerals from waste material, improving recuperation rates.
Furthermore, in wastewater therapy, foam development can show the presence of raw material, functioning as an essential parameter for process tracking. The capability to regulate foam is essential for preserving process security and maximizing functional prices. Understanding the role of foam in industrial applications enables designers and drivers to apply reliable foam management strategies, guaranteeing that foam contributes positively to general process performance while reducing its prospective disadvantages.
Typical Difficulties of Foam Formation
Lots of markets deal with considerable difficulties because of the unintentional formation of foam during numerous procedures. Foam can interfere with the performance of procedures, causing enhanced downtime and higher operational costs. In sectors such as drugs, food and drink, and wastewater treatment, foam can hinder mixing, lower item yield, and complicate separation procedures.
In addition, foam can produce security risks by obstructing clear visibility, which is critical in settings where exact measurements and tracking are necessary. The visibility of foam can likewise result in equipment damages, as extreme pressure accumulation may occur in activators and storage tanks.
Additionally, the need for constant treatment to manage foam can divert sources and labor, eventually affecting performance. Environmental regulations posture one more obstacle, as extreme foam can cause non-compliance issues in effluent discharge, demanding extra treatment processes.
Effect On Item High Quality
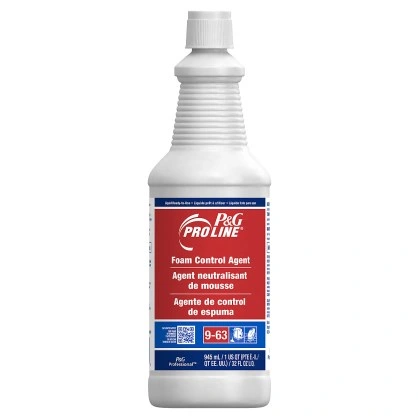
In chemical manufacturing, foam can prevent reaction kinetics by restricting gas-liquid call, resulting in insufficient reactions and lower returns. This not just impacts the effectiveness of manufacturing but can likewise cause second-rate final result that do not meet regulative criteria or customer specs.
Additionally, in drugs, foam formation during formula procedures can present air bubbles right into sensitive compounds, jeopardizing medicine efficiency and security. In addition, foam can trigger functional problems such as overflow and tools breakdowns, increasing downtime and maintenance expenses, additionally influencing item top quality and uniformity.
Strategies for Reliable Foam Control
Addressing the challenges posed by foam is important for maintaining product quality across various industrial industries. Effective foam control techniques are vital to alleviate the negative impacts of foam development, which can interrupt operations and compromise product honesty.
Among the key methods includes the choice and application of suitable antifoaming agents. These agents are designed to lower surface area stress and prevent bubble formation, and their effectiveness can differ based upon the particular process problems. Normal tracking of foam levels is crucial to ensure prompt treatment, allowing drivers to use antifoaming agents before foam comes to be a considerable issue.
Additionally, maximizing process parameters such as temperature level and anxiety can play a vital role in foam monitoring. Minimizing see this page agitation strength or changing feed prices can lessen foam generation. Executing mechanical foam control tools, such as foam breakers or defoamers, can likewise provide efficient services for high-foaming applications.
Educating workers on foam monitoring methods and the significance of keeping optimal operating problems further boosts foam control efforts. Foam Control. By utilizing a mix of these methods, industries can successfully take care of foam, guaranteeing functional efficiency and keeping the quality of their products
Future Patterns in Foam Monitoring
How will developments in modern technology form the future of foam management in industrial procedures? The assimilation of artificial intelligence (AI) and artificial intelligence will transform foam control methods, making it possible for real-time surveillance and adaptive reactions to foam formation. These innovations can examine functional criteria and historical data to predict foam behavior, allowing for preemptive steps that improve process effectiveness.
Furthermore, the advancement of sophisticated foam control agents, including bio-based and ecologically pleasant alternatives, is gaining traction. These innovations not just minimize foam yet additionally straighten with sustainability objectives, minimizing click the environmental footprint of industrial procedures.
Automation will certainly likewise play an important function, as automated foam control systems can enhance the dosage of defoamers based upon real-time dimensions, reducing waste and enhancing effectiveness.
In addition, the fostering of IoT useful link (Web of Things) tools will certainly help with seamless interaction between equipment and foam control systems, ensuring an all natural technique to foam management. (Foam Control)
Verdict
Finally, efficient foam control is important for maximizing commercial processes throughout different sectors. The obstacles positioned by foam development can substantially impact item high quality and functional effectiveness. Implementing critical foam administration techniques, consisting of making use of antifoaming representatives and process optimization, alleviates these challenges. As markets continue to develop, recurring improvements in foam control technologies will better improve performance and sustainability, making sure conformity with environmental guidelines while maintaining the stability of items.
In the food industry, foam stabilization is vital throughout processes like whipping cream or creating beer, where the high quality of foam straight influences consumer perception and product attributes.
Recognizing the role of foam in industrial applications enables drivers and designers to apply reliable foam management strategies, guaranteeing that foam contributes positively to general procedure efficiency while lessening its possible downsides.
Normal surveillance of foam degrees is crucial to ensure timely intervention, allowing operators to apply antifoaming representatives prior to foam becomes a significant concern.
Implementing mechanical foam control tools, such as foam breakers or defoamers, can additionally give reliable remedies for high-foaming applications.
The assimilation of man-made knowledge (AI) and maker knowing will revolutionize foam control strategies, enabling real-time surveillance and flexible actions to foam formation.
Report this page